As máquinas são utilizadas regularmente na fabricação, construção e em muitos tipos de locais de trabalho industriais. Embora os empregadores tenham o dever de garantir que os trabalhadores tenham um ambiente de trabalho seguro, acidentes com máquinas ainda podem acontecer.
Acidentes com máquinas no local de trabalho podem ocorrer devido a inúmeros fatores. No entanto, muitos incidentes ocorrem como resultado de uma falha na implementação dos procedimentos e precauções de segurança necessários.
Além disso, acidentes com máquinas no local de trabalho podem resultar em sérios ferimentos e até mesmo causar a morte dos trabalhadores envolvidos.
Dependendo do local de trabalho e do projeto, várias peças de máquinas ou equipamentos podem ser usadas, e algumas são mais perigosas do que outras.
Por exemplo, trabalhadores da área de construção civil, podem trabalhar com serras de mesa, lixadeiras, máquinas de perfuração ou outros equipamentos elétricos.
Nesse sentido, ainda podem operar máquinas pesadas, incluindo guindastes, empilhadeiras, valetas, escavadeiras, caminhões basculantes e escavadeiras.
Por isso, é fundamental manter o ambiente de trabalho seguro e tentar evitar ao máximo os acidentes com máquinas na empresa.
Acidentes com máquinas e equipamentos no ambiente de trabalho
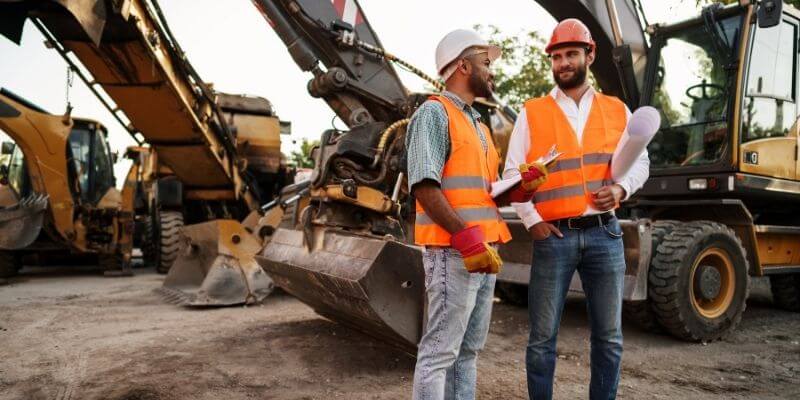
Embora trabalhar com qualquer máquina ou equipamento perigoso sempre apresenta algum risco, às vezes podem existir certas condições que podem
Além dos perigos da proteção de máquinas, outras razões comuns podem incluir acidentes com máquinas no local de trabalho, entre elas:
- Falta de equipamento de proteção;
- Treinamento inadequado;
- Iluminação deficiente;
- Fadiga do operador;
- ;
- Falha na supervisão;
- Defeito de funcionamento da máquina.
Por isso, os empregadores devem garantir que as máquinas e equipamentos do local de trabalho estejam em boas condições de trabalho e que a área ao redor esteja livre de perigos.
Eles também têm a obrigação de fornecer equipamento de proteção pessoal apropriado para a tarefa específica que o trabalhador foi designado e garantir que todos os trabalhadores recebam treinamento de segurança adequado.
Mesmo quando as estão em vigor, ainda podem ocorrer acidentes devido a defeitos da máquina ou à falha do fabricante em equipar a máquina com um aviso de segurança adequado.
Nesses casos, contra o fabricante sob uma teoria de responsabilidade pelo produto.
O que é considerado acidente de trabalho?
é aquele que decorre do exercício profissional e que causa lesão corporal ou perturbação funcional que provoca a perda ou redução, permanente ou temporária, da capacidade para o trabalho.
Porque a segurança das máquinas é importante? A movimentação de máquinas pode causar ferimentos de muitas maneiras, entre elas:
As pessoas podem ser atingidas e feridas por peças móveis de máquinas ou material ejetado. Partes do corpo também podem ser arrastadas ou presas entre cilindros, correias e polias de acionamento.
Bordas afiadas podem causar cortes e ferimentos por corte, peças pontiagudas podem causar esfaqueamento ou perfuração da pele, e peças de superfície rugosa podem causar fricção ou abrasão.
As pessoas podem ser esmagadas, tanto entre as peças que se movem juntas ou em direção a uma parte fixa da máquina, parede ou outro objeto, e duas peças que se movem uma para a outra podem causar cisalhamento.
Partes da máquina, materiais e emissões (como vapor ou água) podem ser quentes ou frias o suficiente para causar queimaduras e a eletricidade pode causar choque elétrico e queimaduras.
As lesões também podem ocorrer devido à falta de confiabilidade e desenvolvimento de falhas nas máquinas ou quando as máquinas são usadas de forma inadequada por inexperiência ou falta de treinamento.
Quais os riscos de acidentes quando se trabalha com máquinas e equipamentos?
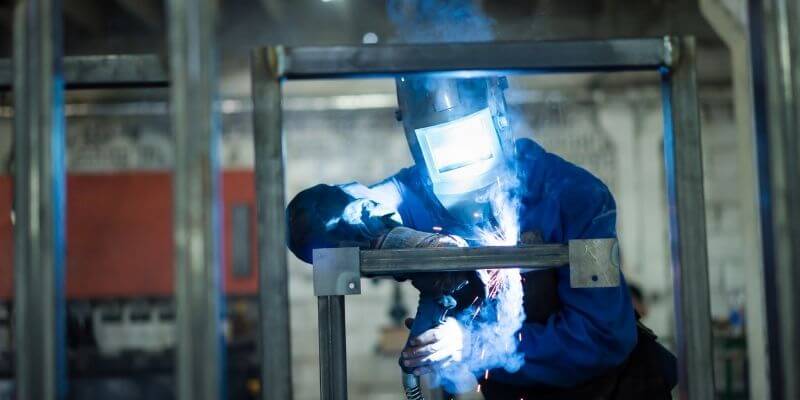
Quais são os riscos de acidentes com máquinas mais comuns? Quando grandes peças de máquinas são utilizadas no local de trabalho, mesmo uma pequena supervisão ou erro pode causar um acidente grave.
Estes acidentes podem incluir uma gama de ferramentas e máquinas, incluindo carregadeiras, guindastes, retroescavadeiras, compactadores, misturadores, empilhadeiras, caminhões de reboque e arados de cabos.
A seguir estão alguns exemplos dos acidentes de trabalho mais comuns envolvendo máquinas pesadas:
Prensamento ou esmagamento de membros
A cada ano, inúmeros que ocorrem quando o corpo é pego ou preso entre dois objetos ou máquinas. Alguns se referem a esses perigos como “pontos de beliscão”.
A força física exercida sobre o corpo preso em um ponto de beliscão pode variar, causando lesões que variam de leves hematomas a partes amputadas do corpo e até mesmo a morte.
Quando seu corpo é esmagado entre dois objetos, as células musculares começam a morrer quase instantaneamente.
Há numerosas causas de lesões por esmagamento no local de trabalho, entre elas:
- Ser atingido por um objeto em queda, como uma grande peça de equipamento;
- Ser afixado ou golpeado entre dois objetos como um pedaço de metal;
- Ser atropelado por máquinas ou equipamentos;
- O colapso de estruturas, tais edifícios em canteiros de obras;
- Membros presos em máquinas;
- Equipamentos ou máquinas tombando, pegando o funcionário;
As lesões por esmagamento podem ocorrer em qualquer indústria, mas o mais comumente acontece nos empresas de fabricação, produção e construção.
Choques elétricos
Em um ambiente de trabalho, um operador de máquina pode receber um choque diretamente com a máquina com a qual está trabalhando, ou ser carregado por indução enquanto está no campo elétrico de um objeto.
A carga se acumula até o operador tocar uma parte aterrada da máquina, e depois descarrega, resultando em um choque.
Novamente, é improvável que leve a qualquer dano grave, mas se o choque for forte o suficiente para causar uma reação de recuo, então podem ocorrer acidentes quando o operador colide com um colega, com uma estrutura da máquina, ou tropeça no caminho de outras máquinas, resultando em ferimentos.
A eliminação do risco de choque é importante para evitar lesões e para mostrar o devido cuidado e atenção ao bem-estar do pessoal. Há, no entanto, outros aspectos subjacentes.
Primeiramente, quando alguém recebe um choque, a máquina envolvida deve ser parada para investigar a causa. Isto resultará em tempo parado e perda de produção.
Se o choque for suficientemente forte para que o receptor precise de cuidados médicos, então a máquina não poderá ser reiniciada até que seja verificada por especialistas em saúde e segurança.
A produção pode ser ainda mais afetada se estes choques estiverem acontecendo com os operadores regularmente, pois as pessoas trabalharão intuitivamente a um ritmo mais lento se perceberem que estão correndo o risco de um choque.
Ninguém gosta de sentir dor e a constante ameaça de choques resultará em uma força de trabalho insatisfeita e infeliz.
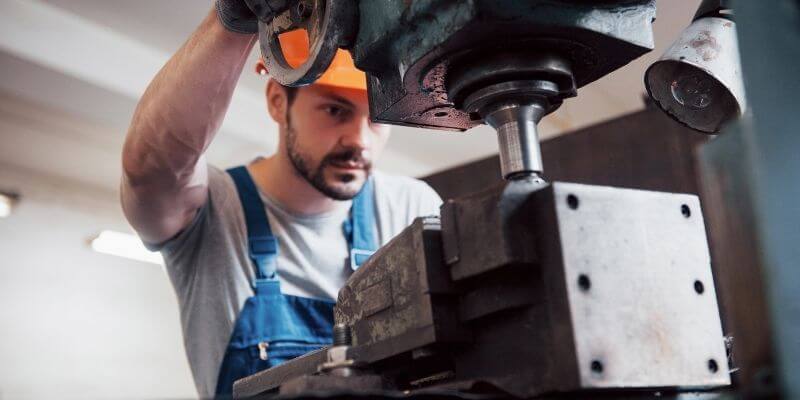
Intoxicação por gases ou vapores
Às vezes será necessário que o onde que há dispersão de contaminantes no ambiente. O perigo principal com o monóxido de carbono é que ele não pode ser facilmente detectado.
O monóxido de carbono é um gás incolor, inodoro e insípido e, portanto, não dá a suas vítimas nenhum aviso prévio.
O monóxido de carbono vem da queima incompleta de gasolina, madeira, carvão, petróleo, gás propano ou qualquer outra coisa que contenha carbono.
O gás venenoso consiste de apenas dois elementos, carbono e oxigênio, e se mistura prontamente com o ar.
O envenenamento ocorre inteiramente pela inalação do composto tóxico do ar. Quando misturado com o ar, grandes quantidades de monóxido de carbono podem ser altamente inflamáveis e explosivas, mas situações que resultam em concentrações tão altas são raras.
O motor de combustão interna é a principal fonte de exposição do local de trabalho ao monóxido de carbono. Muitos fornos e fornos também produzem grandes quantidades de gás, especialmente quando não são mantidos adequadamente.
Motoristas de caminhão, operadores de empilhadeiras ou qualquer pessoa que trabalhe próximo a tais equipamentos estão potencialmente expostos.
Especialmente em perigo estão as pessoas que trabalham perto ou dentro de áreas fechadas, tais como garagens, túneis, docas de carga, armazéns e oficinas de reparação de veículos.
Corte e perfuração de membros
Esse tipo de acidente de trabalho ocorre muitas vezes devido a momentos de distração do próprio trabalhador, isto é, falha humana ao desempenhar tarefas que exigem o manuseio de equipamentos cortantes/pesados.
Uma alternativa é o uso de luva que é um dos principais EPIs no mercado. Hoje há sempre uma solução para a sua atividade, quer seja de baixo, médio ou alto risco; a que tenha somente um risco ou uma série de riscos combinados.
O importante é que a luva seja um importante complemento do trabalho, e que a mesma não atrapalhe, ou gere mais problemas devido ao uso
Projeções de partículas ou peças
Em fábricas que apresentam máquinas como esmeril, lixadeira ou politriz, o e peças é sempre iminente.
Ainda que os funcionários sejam treinados para a ocupação, distrações ou mesmo falhas de equipamento podem causar acidentes graves.
Os cuidados em situações de projeções abruptas devem ser redobrados através da correta proteção do rosto, mãos e olhos.
Os EPIs devem estar em dia: coletes, viseiras, macacões, capacetes e óculos para a proteção do corpo.
Queda
Esse , porque trabalho em altura é uma atribuição presente a quase todos os tipos de indústria.
Em geral, o alto número de quedas é causado por negligência dos colaboradores no que se refere ao uso dos EPIs, em atos imprudentes sob grande risco.
Diversas vezes, os trabalhadores avaliam determinadas situações – ainda que em altura – como simples e rápidas, e abdicam do uso da proteção correta e adequada oferecida pelos EPIs.
Aprisionamento
Em relação ao uso de máquinas e equipamentos, propriamente ditos, a principal recomendação para evitar acidentes de trabalho é respeitar os limites e indicações do uso das máquinas.
Desse modo, o profissional conseguirá diminuir o risco de aprisionamento por erro humano.
Como se livrar dos perigos dos acidentes com máquinas?
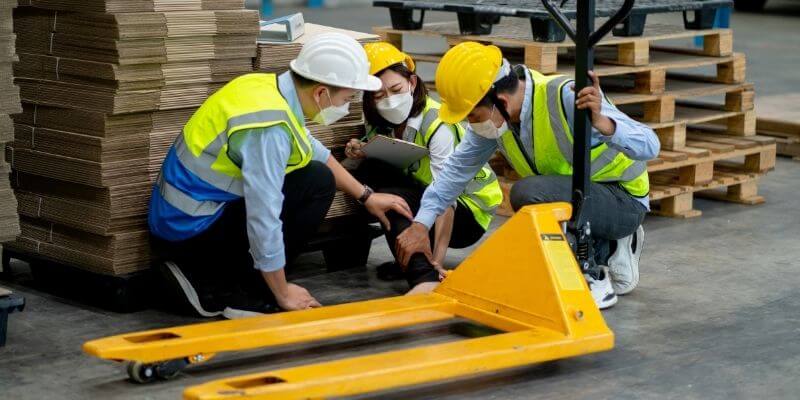
Dependendo da peça de maquinaria que está sendo usada, ela pode causar uma série de ferimentos, desde cortes e contusões menores até ferimentos graves e fatais com risco de vida.
Muitos desses ferimentos podem ser evitados se trabalhadores e empregadores fizerem da segurança uma prioridade máxima em todos os momentos.
Entretanto, mesmo quando os trabalhadores seguem protocolos de segurança, há momentos em que as máquinas estão defeituosas ou não funcionam corretamente.
Qualificação técnica da equipe
As organizações estão sempre em busca de funcionários tecnologicamente aptos porque trabalham mais rápido e de forma mais inteligente. A realização de qualquer trabalho requer o uso de múltiplos conjuntos de habilidades.
Muitos trabalhos exigem habilidades relacionadas a ferramentas físicas ou digitais. As habilidades técnicas são importantes porque quase todo trabalho depende de diferentes ferramentas, programas e processos.
As podem dar a capacidade de oferecer soluções de baixo custo e alta tecnologia que resolvem problemas do mundo real para empregadores de todos os setores.
Além de economizar dinheiro, os funcionários com o conjunto certo de habilidades também economizam tempo, resolvendo problemas mais rapidamente.
Fiscalização constante e eficaz dos trabalhos realizados
Antes de um colaborador começar a usar qualquer máquina, eles precisam pensar sobre quais riscos podem ocorrer e como eles podem ser gerenciados. Portanto, eles devem fazer o seguinte:
- Verificar se a máquina está completa, com todas as proteções instaladas e livre de defeitos.
- Produzir um sistema de trabalho seguro para a utilização e manutenção da máquina. A manutenção pode exigir a inspeção de características críticas onde a deterioração poderia causar um risco.
- Eles também devem observar os riscos residuais identificados pelo fabricante nas informações/instruções fornecidas com a máquina e certificar-se de que estão incluídos no sistema seguro de trabalho.
- Certifique-se de que toda máquina estática foi instalada corretamente e que está estável.
- Escolha a máquina certa para o trabalho e não coloque máquinas onde os clientes ou visitantes possam estar expostos a riscos.
Certifique-se de que a máquina esteja:
- Segura para qualquer trabalho que tenha que ser feito durante a instalação, durante o uso normal, na limpeza de bloqueios, na realização de reparos para avarias, e durante a manutenção planejada;
- Desligada, isolada ou bloqueada adequadamente antes de tomar qualquer ação para remover bloqueios, limpar ou ajustar a máquina;
Além disso, certifique-se de que eles identifiquem e lidem com os riscos de:
- Fontes de alimentação elétrica, hidráulica ou pneumática;
- Proteções mal projetadas.
Manutenção das máquinas e equipamentos utilizados
A finalidade da manutenção do equipamento na fabricação é simples: minimizar as avarias e garantir que as máquinas operem em sua máxima funcionalidade.
Ao garantir a manutenção adequada do equipamento, o elemento surpresa na forma de falha da máquina é virtualmente removido das instalações.
A manutenção regular do equipamento, e a garantia de que os componentes gastos da máquina sejam tratados com antecedência, não só prolonga a vida útil da máquina, mas também diminui a chance de acontecer algum acidente.
Afinal, as máquinas têm componentes que estão sujeitos a desgaste. Juntas, vedações e até mesmo motores devem ser substituídos após um determinado número de horas de uso, e falharão completamente se não forem trocados dentro do tempo adequado.
Ao garantir que todos esses componentes façam parte de um cronograma de manutenção preventiva para substituição, o risco de paradas não planejadas é quase eliminado.
Normas Regulamentadoras que ajudam na prevenção de acidentes com máquinas
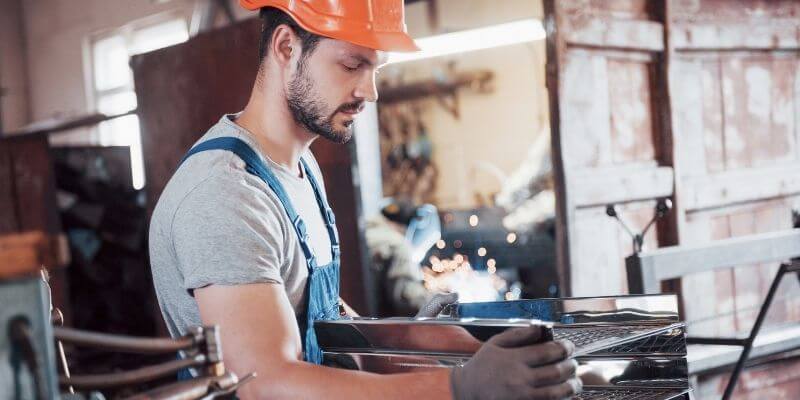
- NR 12 – Máquinas e Equipamentos
A principal norma regulamentadora que trata sobre os acidentes com máquinas e equipamentos é a NR-12.
Esta norma define quais medidas de segurança devem ser adotadas durante a instalação, operação e manutenção de máquinas e equipamentos.
- NR 13 – Caldeiras e Vasos de Pressão
Previne acidentes de trabalho durante a instalação, operação e manutenção de caldeiras e vasos de pressão através de alguns requisitos técnicos.
- NR 14 – Fornos
Estabelece medidas preventivas de riscos durante a fabricação, operação e manutenção de fornos industriais.
Consultoria para evitar acidentes com máquinas com a Engenharia Adequada
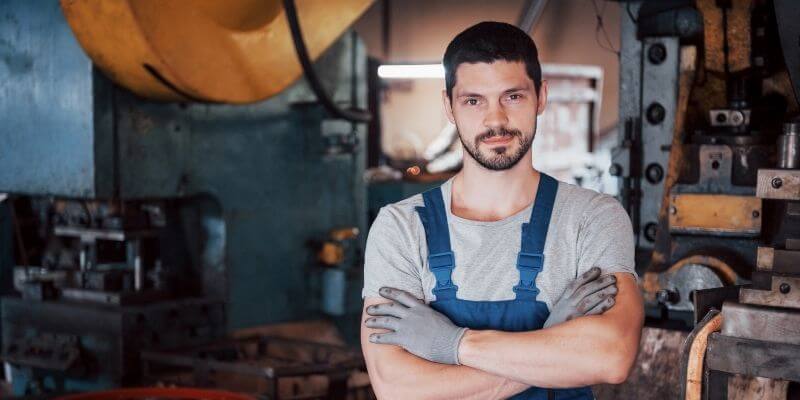
A Engenharia Adequada as melhores soluções de adequação em máquinas e equipamentos conforme a NR12.
Além disso, nossa empresa pode te ajudar a reconhecer os tipos gerais de perigos para proteger as pessoas, os equipamentos e o meio ambiente.
Conduzimos a adequação à NR12 de maneira completa, atuando no planejamento, documentação, execução e treinamentos. Prestamos serviços de consultoria, manutenção, cursos e treinamentos, bem como análise de documentações.
Quer saber mais? Entre em contato conosco.
Também oferecemos um guia prático, gratuito e definitivo construído a partir do método que já adequou a NR12 em mais de 10 mil máquinas e equipamentos em todo o Brasil.
Conclusão

Como empregador é importante desenvolver, implementar, treinar e garantir que os trabalhadores utilizem práticas de trabalho seguras.
Além disso, é necessário equipar as máquinas com proteções devidamente projetadas e construídas e/ou dispositivos de proteção devidamente aplicados e ajustados.
Desse modo, será mais fácil manter a empresa segura e evitar acidentes com máquinas.
Convidamos você a saber mais sobre nosso painel elétrico devidamente regulamento com a NR12 acessando nossa loja virtual. Ou se preferir acesse nosso site e confira mais informações.